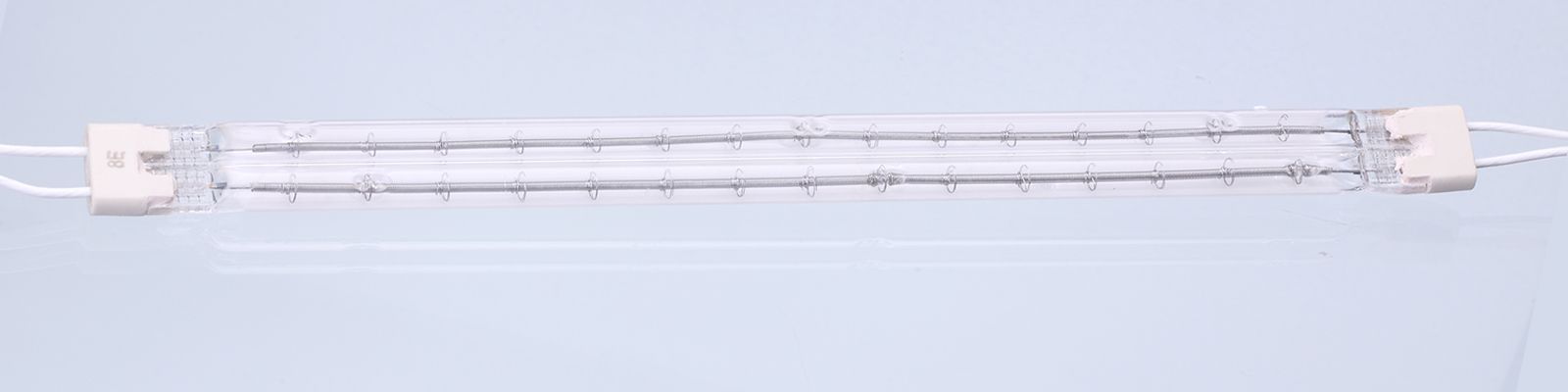
Infrared Emitters: Revolutionizing Printing Ink Drying
In the fast-paced world of printing, efficient drying methods are paramount. Among available techniques, infrared emitters shine as a highly effective option for printing ink manufacturers. These innovative devices not only accelerate drying times but also enhance overall productivity and quality.
Uniform Drying, Consistent Results
Infrared emitters ensure uniform drying across various substrates, a critical factor for printing ink manufacturers. Consistent drying guarantees each product meets stringent quality standards, eliminating inconsistencies.
Sustainable and Energy-Saving
Beyond speed, infrared emitters offer environmental benefits. They not only reduce energy consumption but also minimize the drying process’ environmental footprint. This aligns perfectly with the growing emphasis on sustainability in modern manufacturing.
Deep Penetration, Optimal Drying
A key advantage of infrared emitters is their ability to penetrate deeply into substrates. This ensures thorough drying not only on the surface but also within the material itself, particularly beneficial for inks applied to porous surfaces.
Faster Production, Tighter Deadlines
Infrared emitters facilitate faster production cycles, enabling manufacturers to meet tight deadlines without compromising quality. This flexibility is invaluable in today’s printing industry, where time-to-market is crucial.
Safety First
Infrared emitters enhance drying safety. By eliminating the need for open flames or hot surfaces, these devices reduce the risk of accidents and ensure a safer working environment for employees.
Precise Control, Optimal Results
These emitters offer precise control over drying temperatures, allowing customization for specific ink formulations and substrates. This level of control ensures optimal drying conditions and minimizes the risk of defects or inconsistencies in the final product.
Seamless Integration, Versatile Applications
One of the most significant advantages of infrared emitters is their versatility. They seamlessly integrate into existing printing processes, not only for drying inks but also for coatings and varnishes. This adaptability makes them a cost-effective solution for manufacturers looking to upgrade their drying capabilities.